
What Is YIMUSANFENDI 2023 Best Info About It
August 1, 2023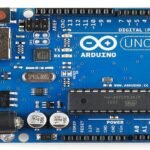
Getting Started with Arduino: Essential Tips and Tricks
January 7, 2025When it comes to getting a smooth, even finish in powder coating, understanding airflow patterns inside powder coating ovens can be the key to success. The flow of air inside these ovens affects how well the coating adheres and cures, which in turn impacts the final product’s durability and appearance. This process involves more than just turning up the heat; it’s about managing airflow dynamics to create consistent temperatures and effective heat transfer. From managing laminar flow to balancing intake and exhaust, airflow science plays a vital role in producing quality results.
Laminar Flow Dynamics for Even Heat Distribution
Imagine a river flowing smoothly downstream—that’s laminar flow, but inside a powder coating oven. In simple terms, laminar airflow is when air moves in parallel layers without much mixing. This is essential for even heat distribution across the coated parts. When the hot air flows smoothly around the parts, it helps maintain a consistent temperature throughout the oven, ensuring that each coated surface receives the same level of heat.
Maintaining laminar flow in powder coating ovens is all about controlling the speed and direction of the air. By keeping the airflow steady, manufacturers can minimize hot and cold spots, which can lead to inconsistent coating thickness or even defects. Think of it like baking a cake; if the oven’s heat isn’t evenly distributed, some parts bake faster than others, resulting in an uneven finish. Proper laminar flow ensures that the coating cures evenly, leading to a better finish and greater durability.
Controlling Turbulence to Prevent Uneven Coating
While laminar flow is ideal, sometimes turbulence is inevitable. Turbulence occurs when the airflow becomes irregular, creating swirling patterns that can disrupt the even distribution of heat. In powder coating ovens, this can be problematic because it leads to uneven curing, which may result in blotchy or inconsistent coatings.
To tackle turbulence, oven design often incorporates features like baffles or deflectors. These components redirect airflow to prevent swirling and keep heat distribution more consistent. Turbulence control is especially important when working with complex parts, where curves and edges can interrupt smooth airflow. Managing this aspect of airflow patterns can make a significant difference in achieving a high-quality, uniform coating.
Strategic Air Vent Placement for Optimal Circulation
The placement of air vents inside powder coating ovens is more strategic than it might seem. Properly positioned air vents help control airflow direction and circulation, ensuring that heat is distributed efficiently throughout the oven. If vents are not placed correctly, the airflow could either be too forceful or too weak, leading to hot spots or under-heated areas that impact coating quality.
By strategically positioning vents near critical points, such as around complex shapes or edges, manufacturers can guide the airflow to reach all surfaces of the coated parts. This improves heat transfer and ensures that even the hardest-to-reach areas are properly cured. It’s like aiming a hairdryer at wet hair—if you miss certain spots, it won’t dry evenly. In powder coating ovens, this means a more thorough and consistent curing process for each part.
Balancing Intake and Exhaust for Pressure Consistency
Achieving the right balance between air intake and exhaust is key to maintaining consistent pressure inside powder coating ovens. This balance prevents sudden pressure changes that could disrupt airflow patterns and affect heat distribution. Too much intake without proper exhaust can create a high-pressure environment, causing air to move erratically. On the flip side, too much exhaust can lead to a vacuum effect, pulling heat away from the parts before the coating fully cures.
To avoid these issues, powder coating ovens are designed to maintain a balanced airflow system. This approach helps keep the temperature steady, enabling an even and reliable curing process. Proper pressure consistency also reduces the risk of contamination from outside air, ensuring that the coating quality remains high.
Vortex Creation and Its Role in Heat Retention
Not all airflow patterns are about straight lines. Sometimes, creating small vortices inside the oven can help retain heat, especially in larger or more complex powder coating ovens. Vortices are swirling air currents that can trap heat, keeping it circulating longer inside the oven. This is particularly useful for thicker parts that require more time to cure, as the retained heat helps ensure complete and even curing.
The trick with vortices is to control their size and location. If the vortex is too large or positioned poorly, it can disrupt overall airflow and create uneven heating. When designed correctly, however, these swirling patterns can be an asset, contributing to a more efficient curing process and better coating results.
Fine-Tuning Velocity to Match Specific Coating Requirements
Different types of coatings and parts require specific airflow velocities to achieve optimal results. For example, lightweight parts with thin coatings may need gentler airflow, while heavier parts with thicker coatings might require stronger airflow to ensure even heat distribution. Powder coating ovens can be adjusted to fine-tune the air velocity, matching the specific requirements of the coating and parts being processed.
Fine-tuning the airflow velocity is like adjusting the flame under a stovetop pan—it has to be just right for what you’re cooking. In the context of powder coating, getting the airflow speed right ensures that the coating adheres properly and cures evenly, reducing the likelihood of defects and increasing the quality of the final product. This kind of customization in airflow dynamics not only improves coating consistency but also boosts overall production efficiency.